|
|
 |
|
 |
For
cranes, Slings, Shovels, Hoists & general Engineering Purposes |
 |
|
|
|
|
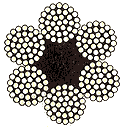 |
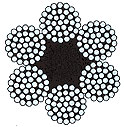 |
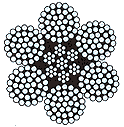 |
(6x37) 8 to 56 mm
With Fibre Core (FC) |
(6x37) 8 to 56 mm
With Fibre Core (FC) |
(6x37) 8 to 26 mm
with Steel Core (IWRC) |
|
 |
|
|
For
Mooring , Heavy derrick, Hoist Ropes, Towing, Oil, well, Drilling
& General Engineering Purposes |
 |
|
|
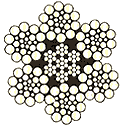 |
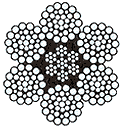 |
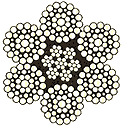 |
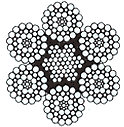 |
6x26 (10/5 & 5/5/1)
(FC) or (IWRC)
9 to 40 mm |
6x36 (14/7 & 7/7/1)
(FC) or (IWRC)
13 to 56 mm |
6x41 (16/8 & 8/8/1)
(FC) or (IWRC)
16 to 60 mm |
6x49 (16/8 & 8/8/1)
(FC) or (IWRC)
48 to 92 mm |
|
 |
|
 |
How
groove depth effects the diameter of wire ropes ? |
The depth of groove should be
selected so that the rope does not rub against the
flange of the sheave or each other while entering
running or leaving the groove. Angle of circular arc
of the bottom of groove should not be less than 120
degrees.
The grooves on the drum should be pitched so that
there is clearance between neighbouring turns of rope
on that drum. The recommended clearances are 1.5 mm up
to rope diameter of 12 mm, 2.5 mm up to rope diameter
of 28 mm and 3mm for rope diameter above 28 mm.
The groove diameter of the pulley or sheave should
always be larger than the actual diameter of the rope.
But if the groove diameter is too large the rope will
tend to flatten and if it is too small pinching of
rope will take place.The correct positioning is
explained along with tolerance and clearances on pully
or sheave groove diameters |
|
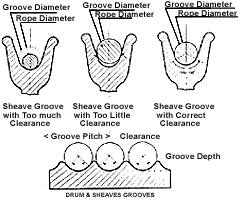 |
|
 |
|
|
|
|
Checks
List before taking ropes into use : |
 |
 |
|
# |
Blocks and sheaves : Please ensure that all
the grooves of the sheaves are in proper alignment and shape
to avoid damage of the ropes. |
# |
Bushings and bearings to be checked
periodically to avoid any ply in the normal working of wire
ropes. |
# |
Check the ship rollers and guides to avoid
damage to the outer strands of the rop. |
# |
Do not jerk load the rope while lowering
the crane blocks |
# |
Dragging of material should be avoided as
it may cause damage to the internal core of the ropes |
# |
You can increase yhe life of the ropes by
proper lubrication and careful handling. |
|
 |
|
|
|
|
|
 |
|