 |
How groove depth effects the diameter of wire ropes
|
|
|
The depth of groove should be selected so that the rope does not rub against the flange of the sheave or each other while entering running or leaving the groove. Angle of circular arc of the bottom of groove should not be less than 120 Degrees.
The grooves on the drum should be pitched so that there is clearance between neighboring turns of rope on that drum. The recommended clearances are 1.5 mm up to rope diameter of 28 mm and 3 mm for rope diameter above 28 mm.
The groove diameter of the pulley or sheave should always be larger then actual diameter of the rope. But if the groove diameter is too large the rope will tend to flatten and if it is too small pinching or rope will take place. The correct positioning is explained as under along with the tolerance and clearances on pully or sheave groove diameters.
|
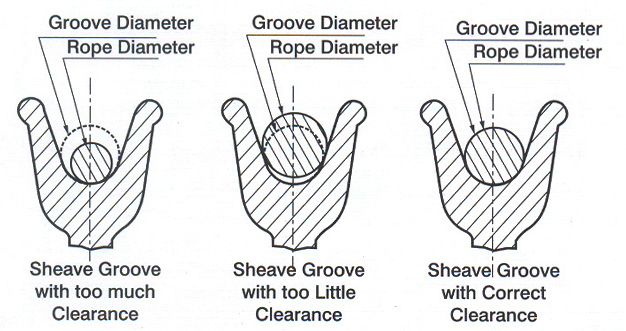 |
Construction |
Minimum Sheave Dia. |
6x19S, 18x7NR |
32 x Dr. |
6 x 19 W, 6x21 FW, 6x26WS |
30 x Dr. |
6x19, 8x19 S, 8x19 W, 8x21 FW |
26 x Dr. |
6 x 25 FW, 6 x 31 WS |
24 x Dr. |
34 x 7 NR |
23 x Dr. |
6x24, 6x36 WS, 8x25 FW |
22 x Dr. |
6x37 |
19xDr. |
Dr. = Rope Diameter S = Seale W = Warrington
FW = Filler Wire WS = Warrington-Seale NR = Non-Rotating
|
|
|
How Sheaves Size Effects Wire Rope Strength
|
The radius of bend has effect on the strength of wire rope. In order to take this fact into account in selecting the size sheave to be used with a given diameter wire rope, the following table can be used as a guide:
Ratio "A" = |
Sheave Dia. Rope Dia. |
Strength Efficiency Compared to Catalog Strength in % |
40 |
|
95 |
30 |
|
93 |
20 |
|
91 |
10 |
|
86 |
8 |
|
83 |
6 |
|
79 |
4 |
|
75 |
2 |
|
65 |
1 |
|
50 |
FOR EXAMPLE :
Using a 1/2 dia. wire rope with a 10" dia sheave, Ratio "A" =10 H- 1/2 = 20 and the strength efficiency = 91% as compared to the catalog strength of wire rope.
Blocks and Sheaves: Please ensure that all the grooves of the sheaves
are in proper alignment and shape to avoid damage of the ropes.
Bushings and Bearings to be checked periodically to avoid any ply in
the normal working of wire ropes.
Check the ship rollers and guides to avoid damage to the outer strands
of the rope
Do not jerk load the rope while lowering the crane blocks.
Dragging of material should be avoided as it may cause damage to the internal core of ropes.
You can increase the life of the ropes by proper lubrication and careful handling.
|
|
The repeated bending and straightening of the wire rope causes a cyclic change of stress known as "fatiguing". The radius of bend has considerable effect on the fatigue life of wire rope and the following can be used as comparison of relative fatigue life as influenced by sheave diameter:
Ratio "B" = |
Sheave Dia. Rope Dia. |
Strength Efficiency Compared to Catalog Strength in % |
30 |
|
10.0 |
26 |
|
6.6 |
20 |
|
3.8 |
18 |
|
2.9 |
16 |
|
2.1 |
14 |
|
1.5 |
12 |
|
1.1 |
FOR EXAMPLE :
Using a 12 dia.. Sheave with a 3/4"dia. wire rope, Ratio "B" = 12+3/4 = 16 and the units of fatigue life = 2.1. However, a 22.5" dia. sheave using a 3/4" wire rope has a Ratio "B" = 225 4- 3/4 =30 and the units of fatigue life = 10. So, The expected extension of fatigue life when using a 22.5" dia. instead of a 12" dia. sheave would be 10 -5- 2.1 or 4.7 times greater. |
|
|
|
|
|
Oval Eye |
Note : If the sheaves are fitted with tappered Roller Bearings, side bearing caps and flat heads screws specially designed by ELTECH should be provided.
|
Item of Gear |
Docks Regulations 1990 |
The Shipbuilding & Ship-repairing Regulations 1990 |
Factories Act 1963 |
The Construction (Lifting Operation) Regulations 1963 |
Chains Rings Hooks Shackles Swivels |
After proof testing and every 12 months. Also inspected before use or in preceding 3 months. |
After proof testing and every 6 months.
Also applicable to Plate Clamps and Eyebolts. |
After proof testing and every 6 months. |
After proof testing and every 6 months. When not in regular use examine only when necessary. Also applicable to Plate Clamps and Eyebolts. |
Blocks |
After proof testing and every 12 months. |
After proof loading and every 6 months. |
After proof testing and every 6 months. |
After proof loading and every 14 months. Inspect in position every week. |
Wire Ropes |
Every 3 months. After broken wires appear, every month |
Every 3 months. After broken wire appear, every month. |
Every 6 months. |
On Cranes Inspect in position every week. Slings After proof loading and every 6 months. When not in regular use, examine only when necessary |
Fiber Rope |
Every 3 months. |
Every 6 months. |
Every 6 months. |
|